GENERATIVE ORTHOSES
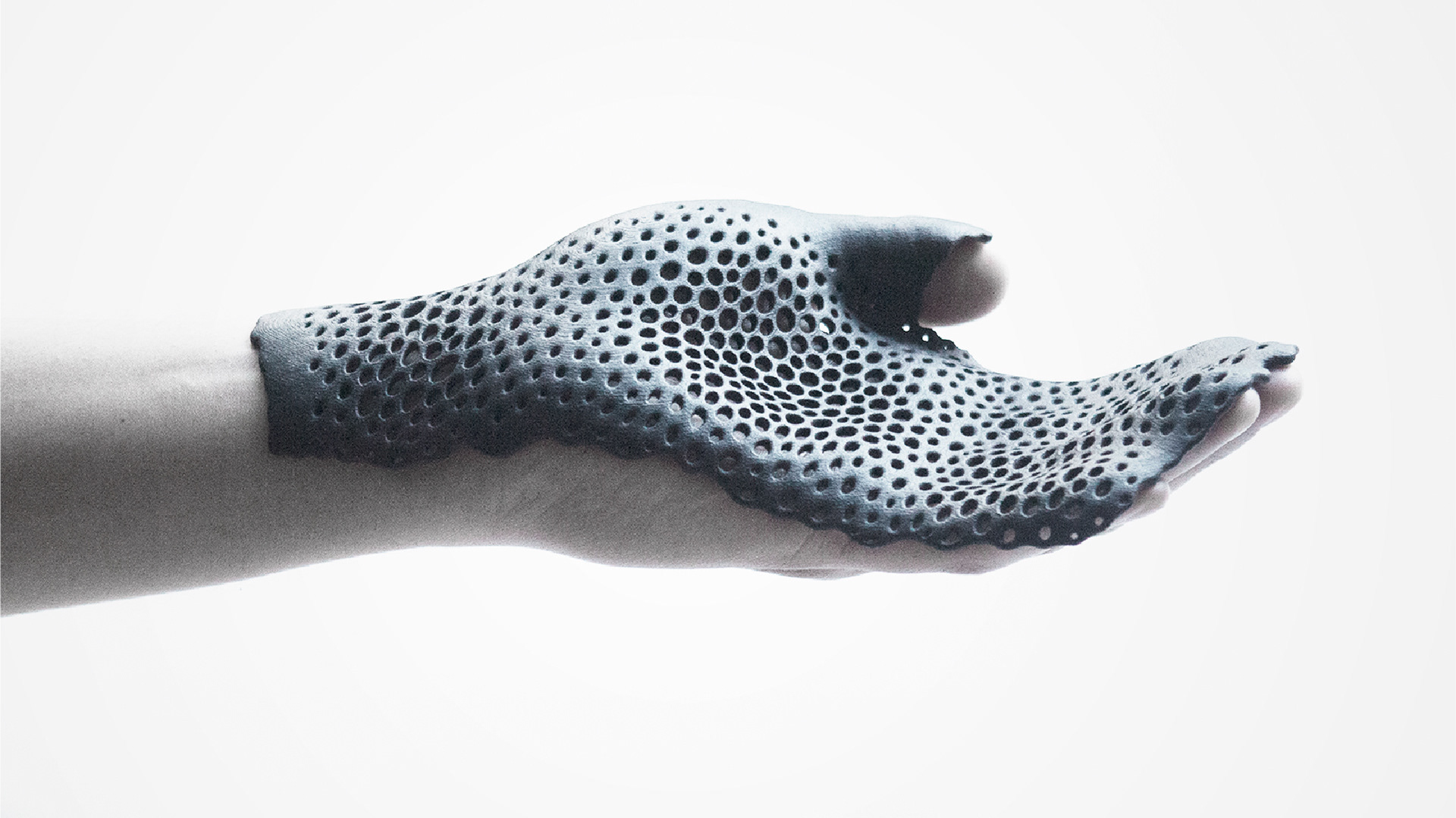
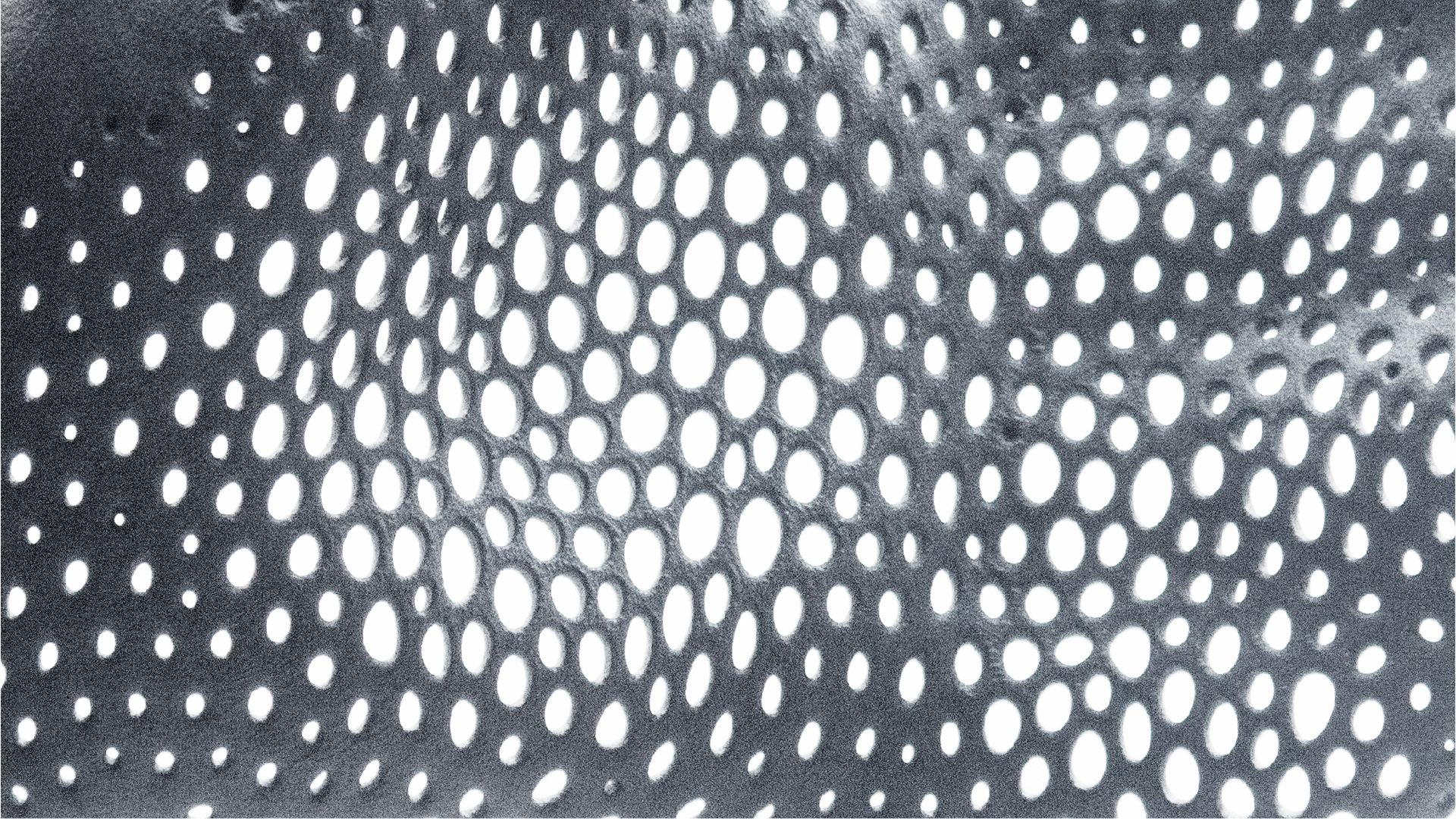
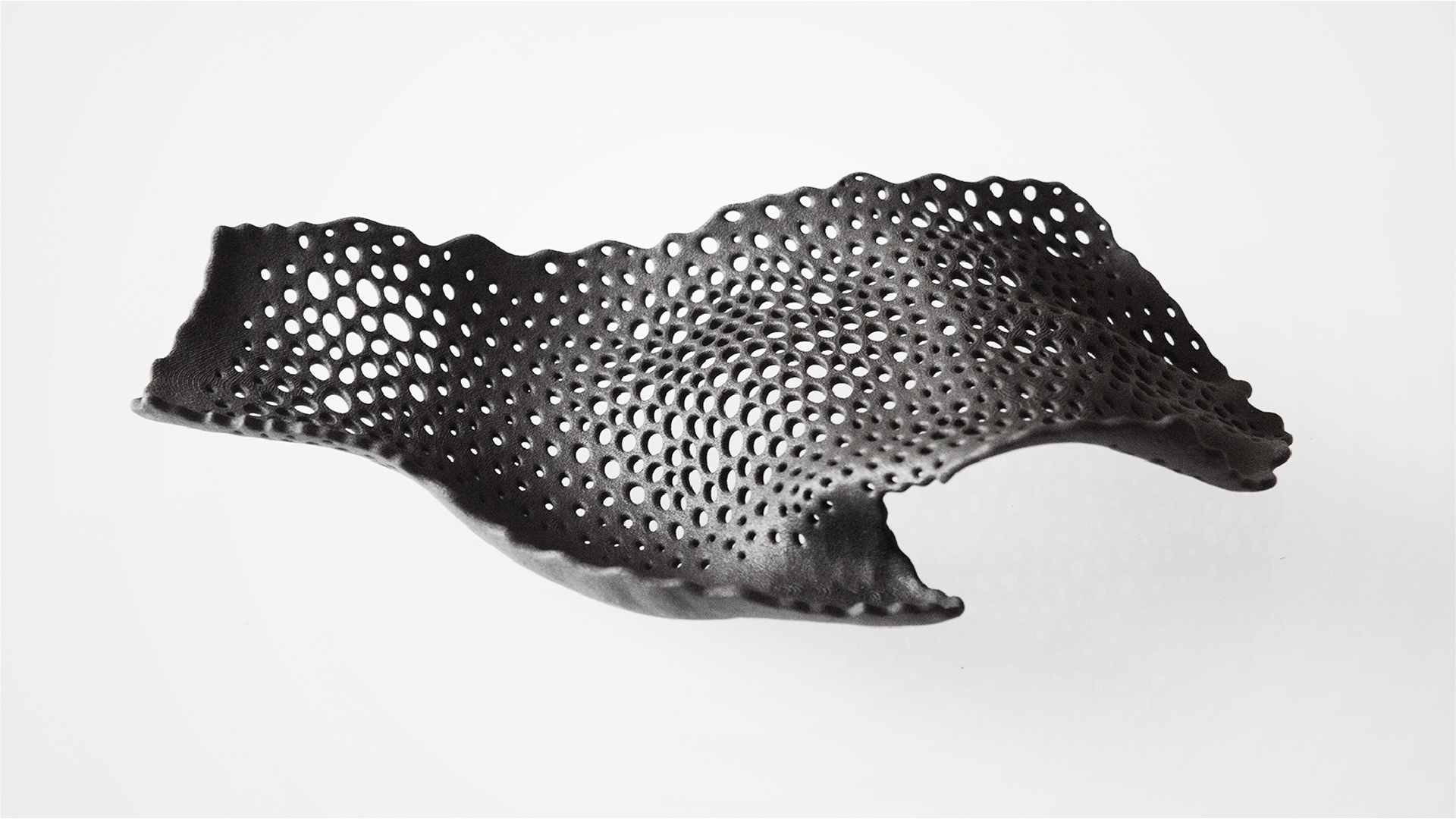
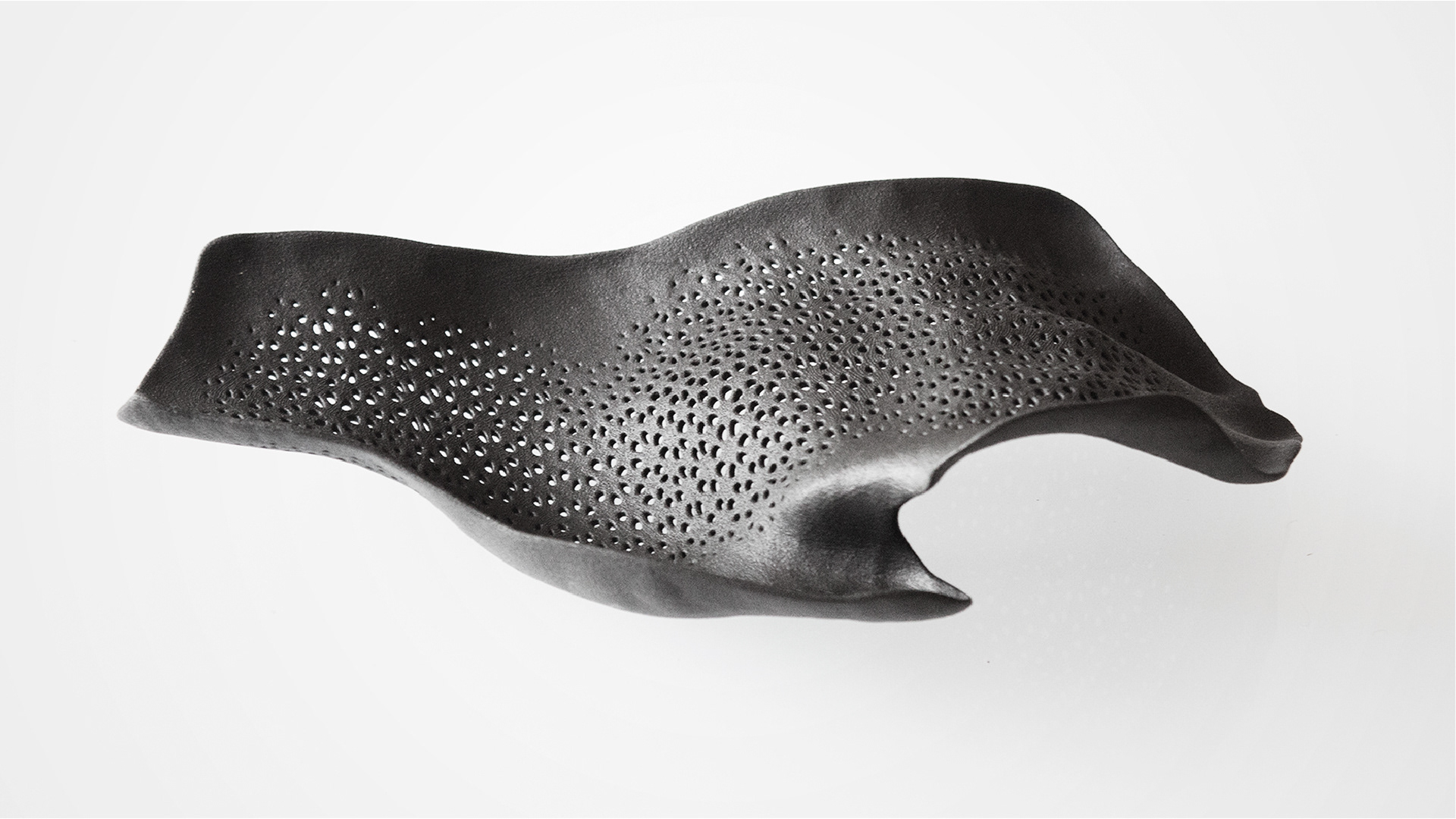
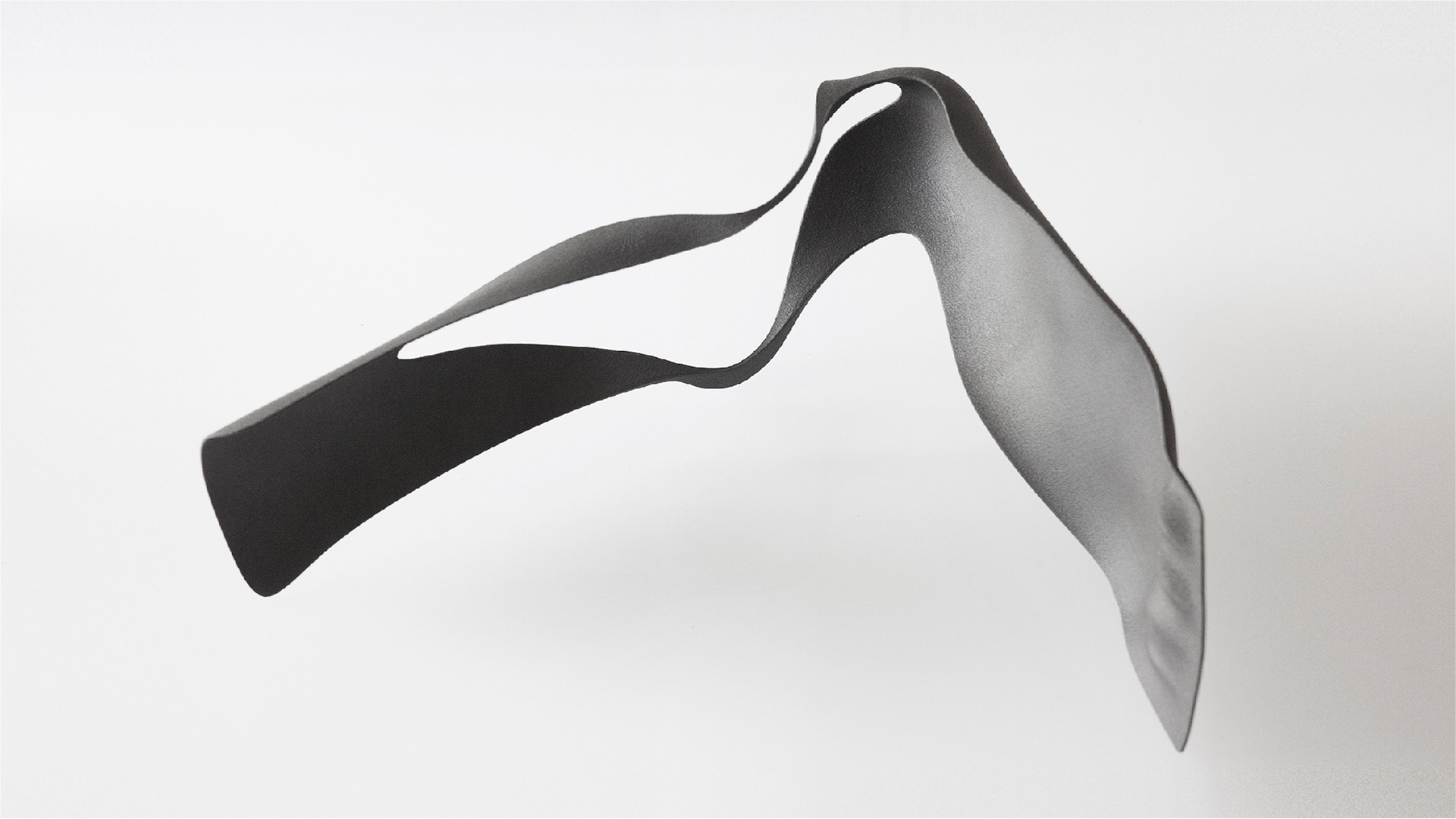
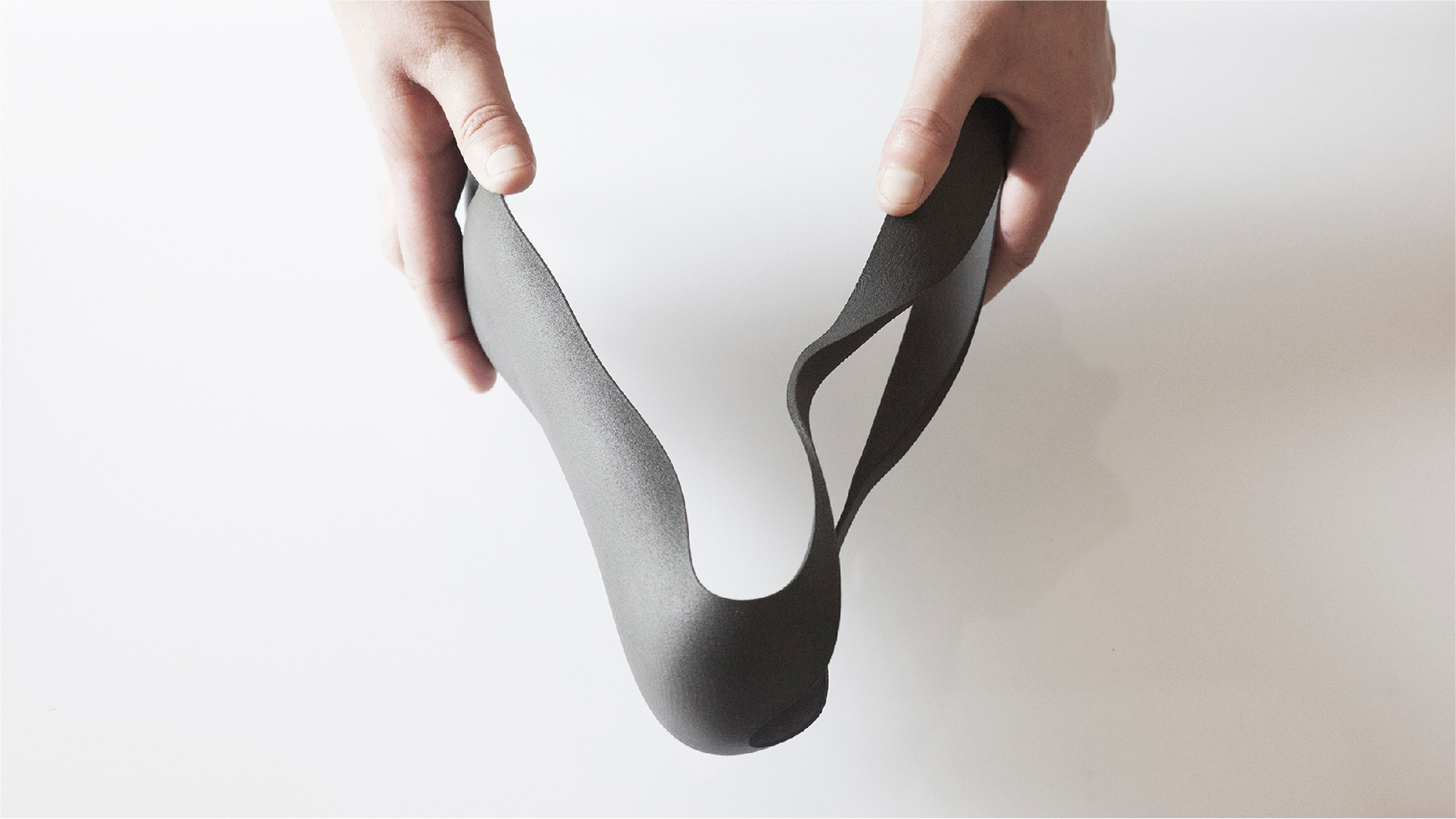
An orthosis is a medical device, applied externally to the human body, used to modify the structural and functional characteristics of the neuromuscular and skeletal system.
Its general purpose is to assist, restrict, control or limit movement for specific body segments, providing support for chronic movement defects, aiding rehabilitation from fractures or surgical operations, correcting the shape or function of the body to extend its capabilities or reduce pain.
Its general purpose is to assist, restrict, control or limit movement for specific body segments, providing support for chronic movement defects, aiding rehabilitation from fractures or surgical operations, correcting the shape or function of the body to extend its capabilities or reduce pain.
MHOX (Filippo Nassetti – Alessandro Zomparelli) and CRP Group, in collaboration with medical professionals, extended the experience of the Collagene masks project developing an integrated framework of mass customization for generative orthoses.
The system is based on three phases: bodyscan of the patient; generation of a 3d model of orthosis; 3d printing of the orthosis. It was developed as an integrated framework for the design of mass customization systems, aiming at replacing the traditional sizes system (XS, S, M, L, XL, XXL) with a complete customization of the product.
The system is based on three phases: bodyscan of the patient; generation of a 3d model of orthosis; 3d printing of the orthosis. It was developed as an integrated framework for the design of mass customization systems, aiming at replacing the traditional sizes system (XS, S, M, L, XL, XXL) with a complete customization of the product.
MHOX designed the first two phases developing a software workflow that integrates the management of scanning sensors, the postproduction of their outputs, and a set of generative algorithms aimed at fitting the device on the patient anatomy and articulating its form to achieve specific, customized performance.
The bodyscan of the patient is performed via infrared or structured light sensors. This phase was designed to be fast, easily manageable in medical environment, cheap in terms of hardware resources.
The generation of a 3d model of orthosis allows the designer to differentiate object's morphology from patient to patient, managing specific performance needs, while adapting to personal anatomies. It is possible to create devices with different balances of stiffness and flexibility, allow certain movements while constraining others, integrate an aesthetic value, implement material properties totally new to this objects, such as porosity and surface articulation.
3D printing and additive manufacturing were used to create the orthosis. This technology can enable the full customization of the medical device according to patient need.
The material that CRP Group used for this kind of application is Windform GT that is a polyamide-based material reinforced with glass fibers. Windform GT is characterised by high flexibility, resistance to liquid and moisture, and it combines elasticity, ductility and resistance. Thus it can be considered a highly valuable material in functional applications affected to vibration and shocks too. In fact, the material has meaningful values of impact strength and elongation at break. It can count on relevant values of tensile strength and flexural strength making it the ideal laser sintering material for the creation of orthosis where resistance to "damage" is a prerequisite.
The additive manufacturing and Windform GT were used to build tailor-made orthosis together with the software developed by MHOX.
The material that CRP Group used for this kind of application is Windform GT that is a polyamide-based material reinforced with glass fibers. Windform GT is characterised by high flexibility, resistance to liquid and moisture, and it combines elasticity, ductility and resistance. Thus it can be considered a highly valuable material in functional applications affected to vibration and shocks too. In fact, the material has meaningful values of impact strength and elongation at break. It can count on relevant values of tensile strength and flexural strength making it the ideal laser sintering material for the creation of orthosis where resistance to "damage" is a prerequisite.
The additive manufacturing and Windform GT were used to build tailor-made orthosis together with the software developed by MHOX.
The software to scan and generate the orthosis is designed to be adaptable to different body segments and performance needs. As of April 2014, it was tested for the development of hand orthoses and leg ones.
The hand orthosis is intended to be a device to aid rehabilitation after surgical operation. It constrains any movement of the hand. A surface porosity, variable in size and distribution, allows the hand to stay ventilated and washable. The combination of the biologically inspired design and material qualities of the 3d printed object produce an aesthetic value new to this devices.
The leg orthosis is a device for patients with peroneal muscles deficits and consequent troubles in their gait cycle. The 3d scan allows the object to embrace both the leg and the foot, directly integrating a plantar. A specific joint, centered on the ankle, whose geometric characteristics vary parametrically from patient to patient, employs the flexibility of the material to provide active support and control in the gait cycle.
The generative framework is designed to be extended to any body segment and a wide variety of generative strategies and algorithms. MHOX and CRP Group look forward to its development connecting generative design sensibilities and 3d printing technologies, targeting different clinical applications and emerging opportunities.