COLLAGENE MASKS
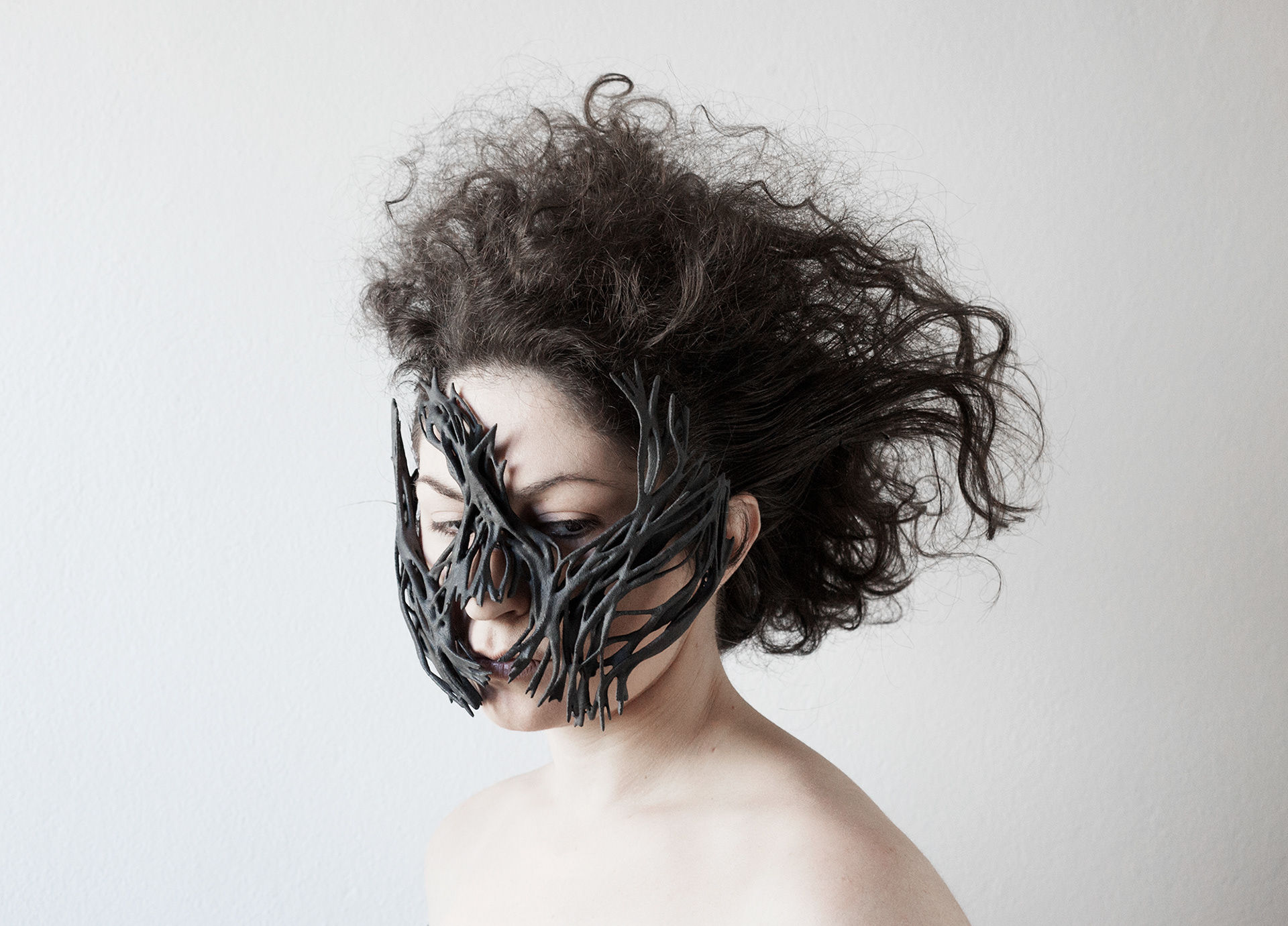
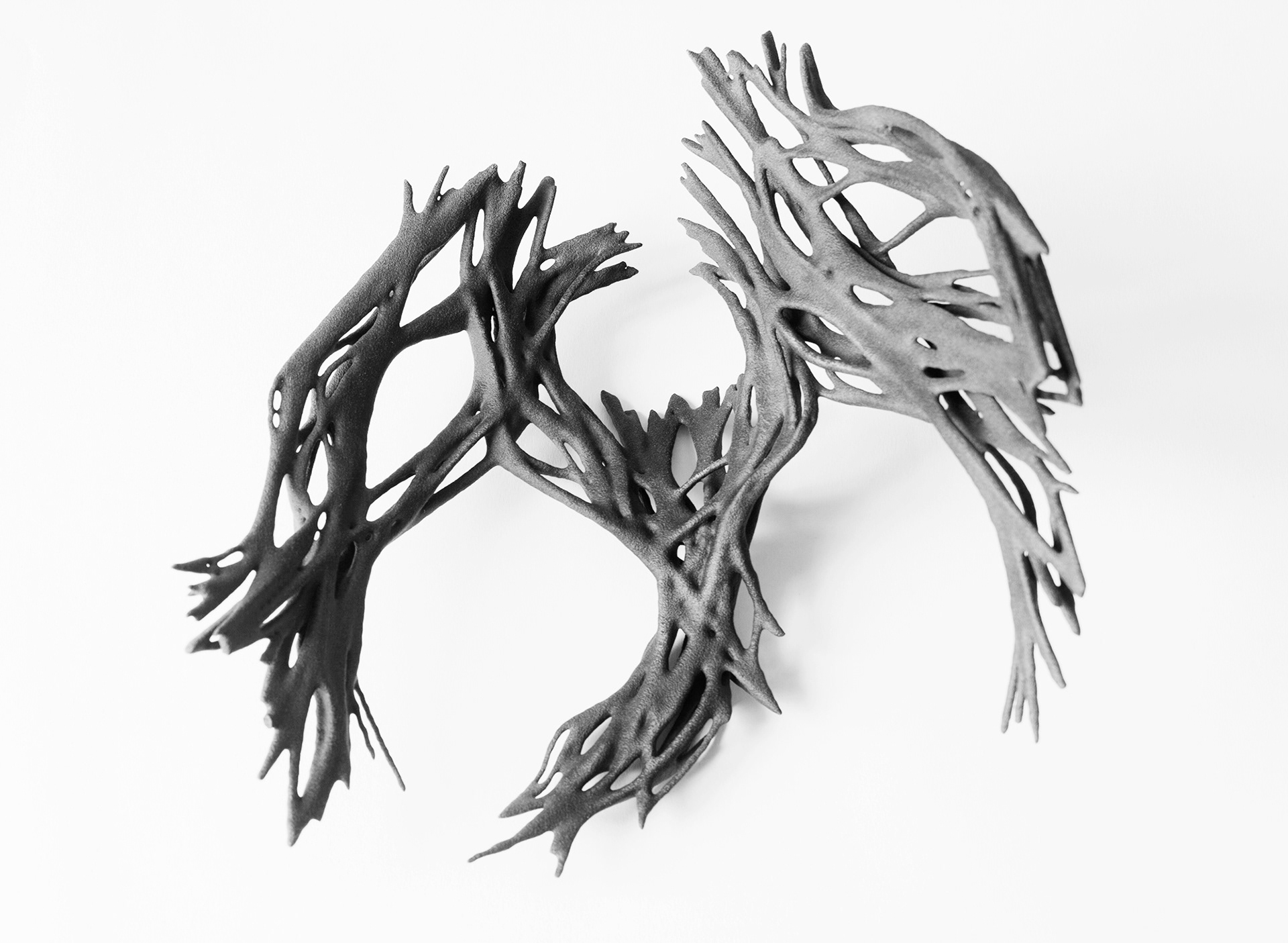
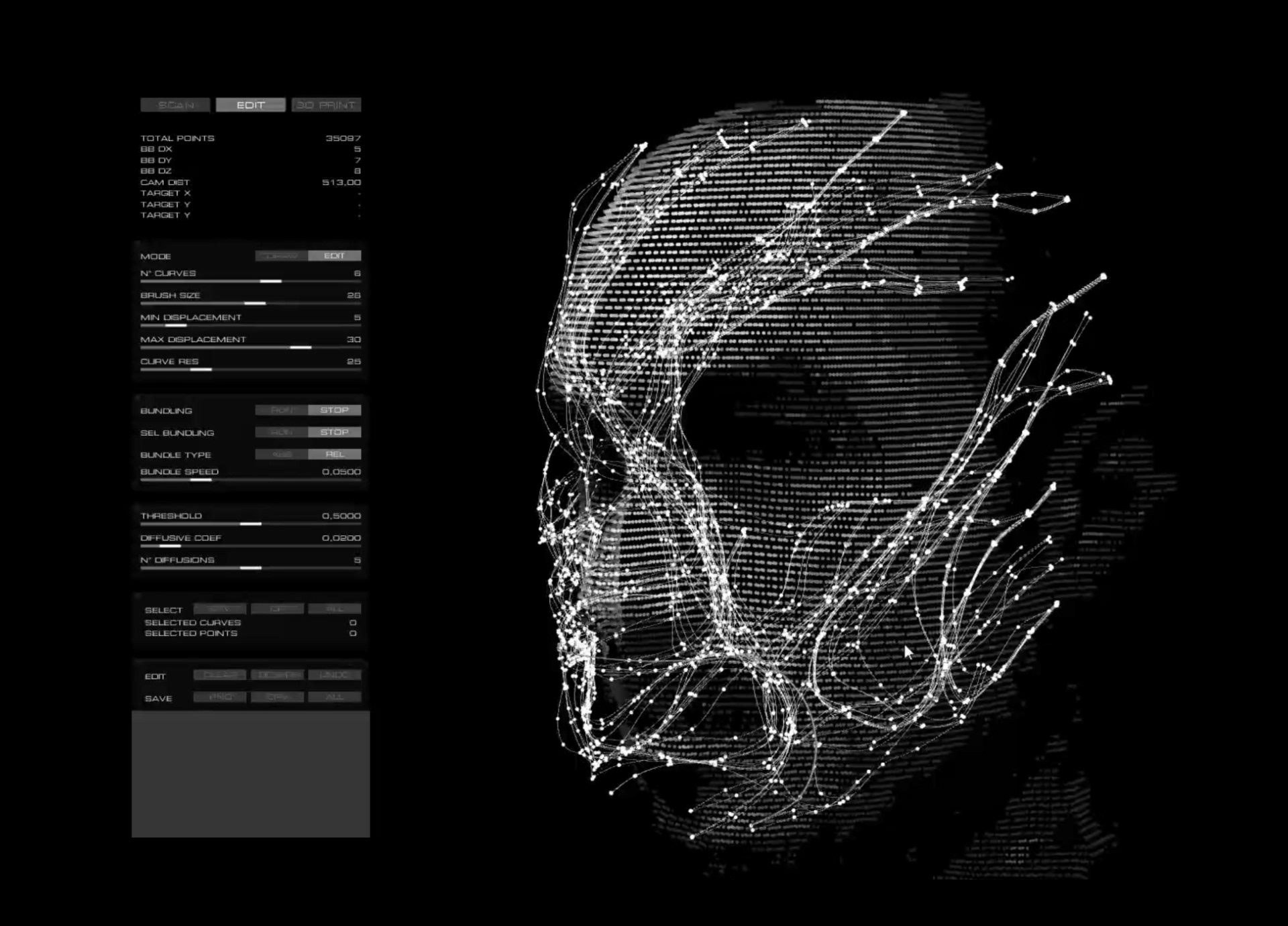
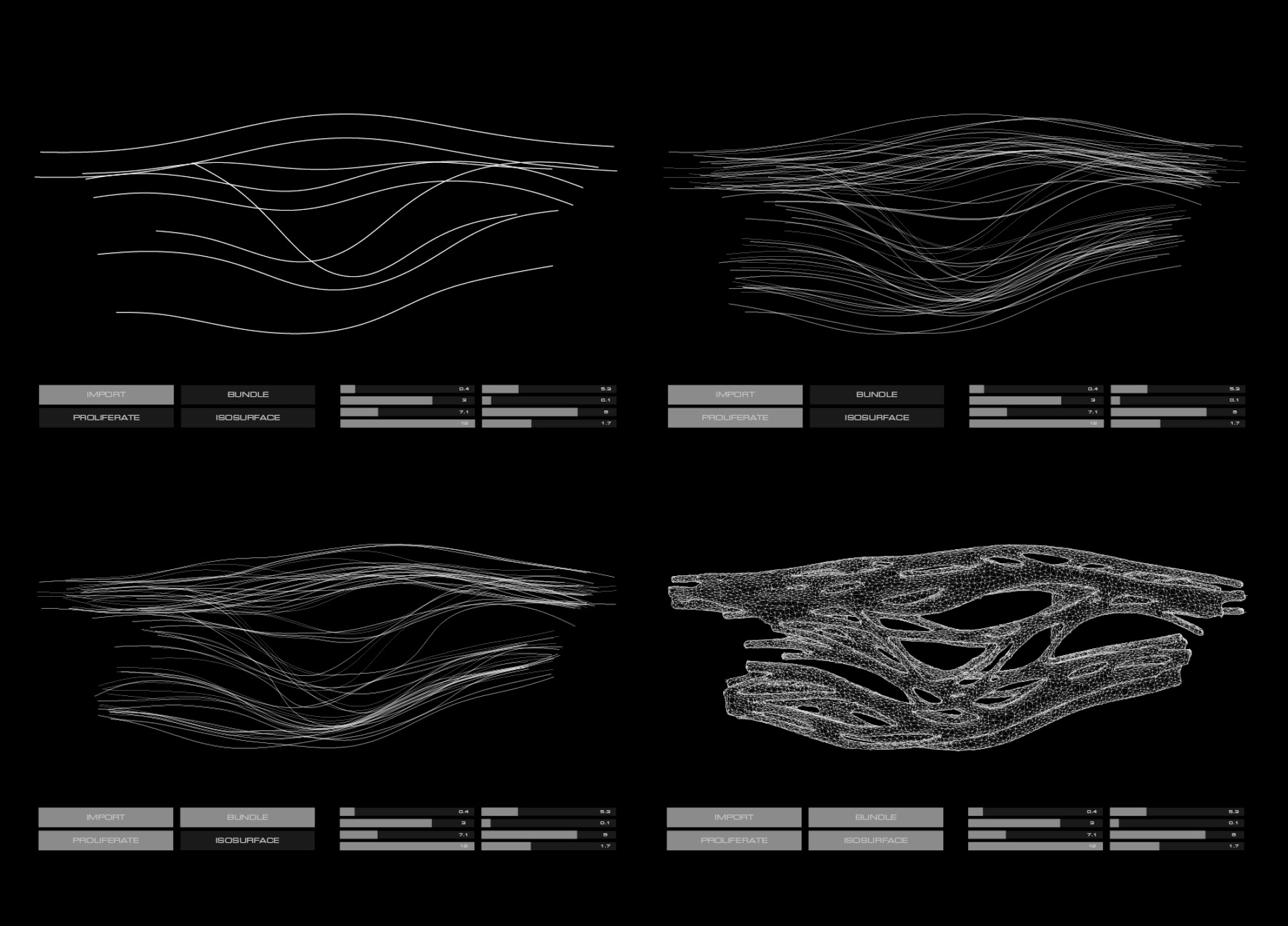
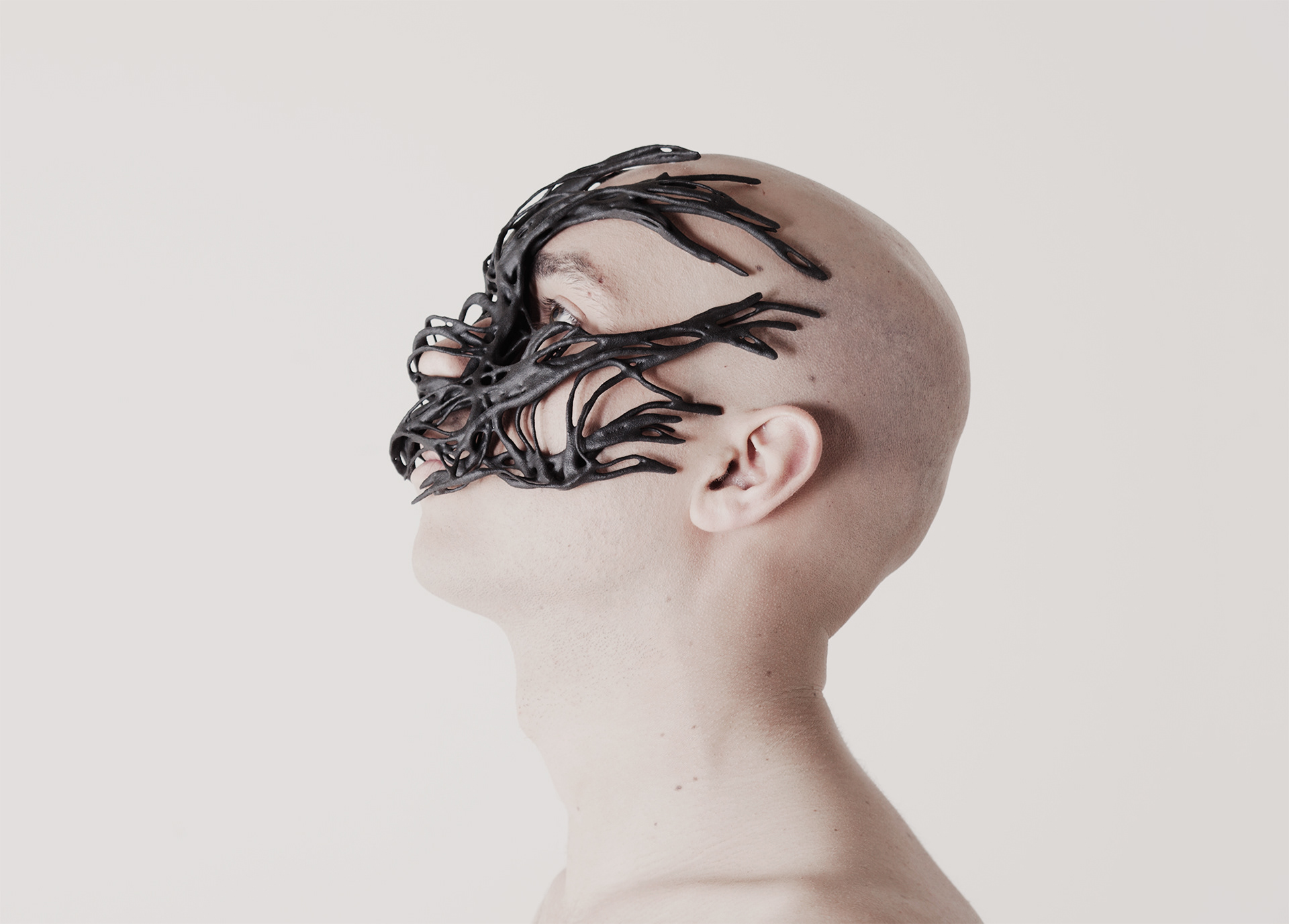
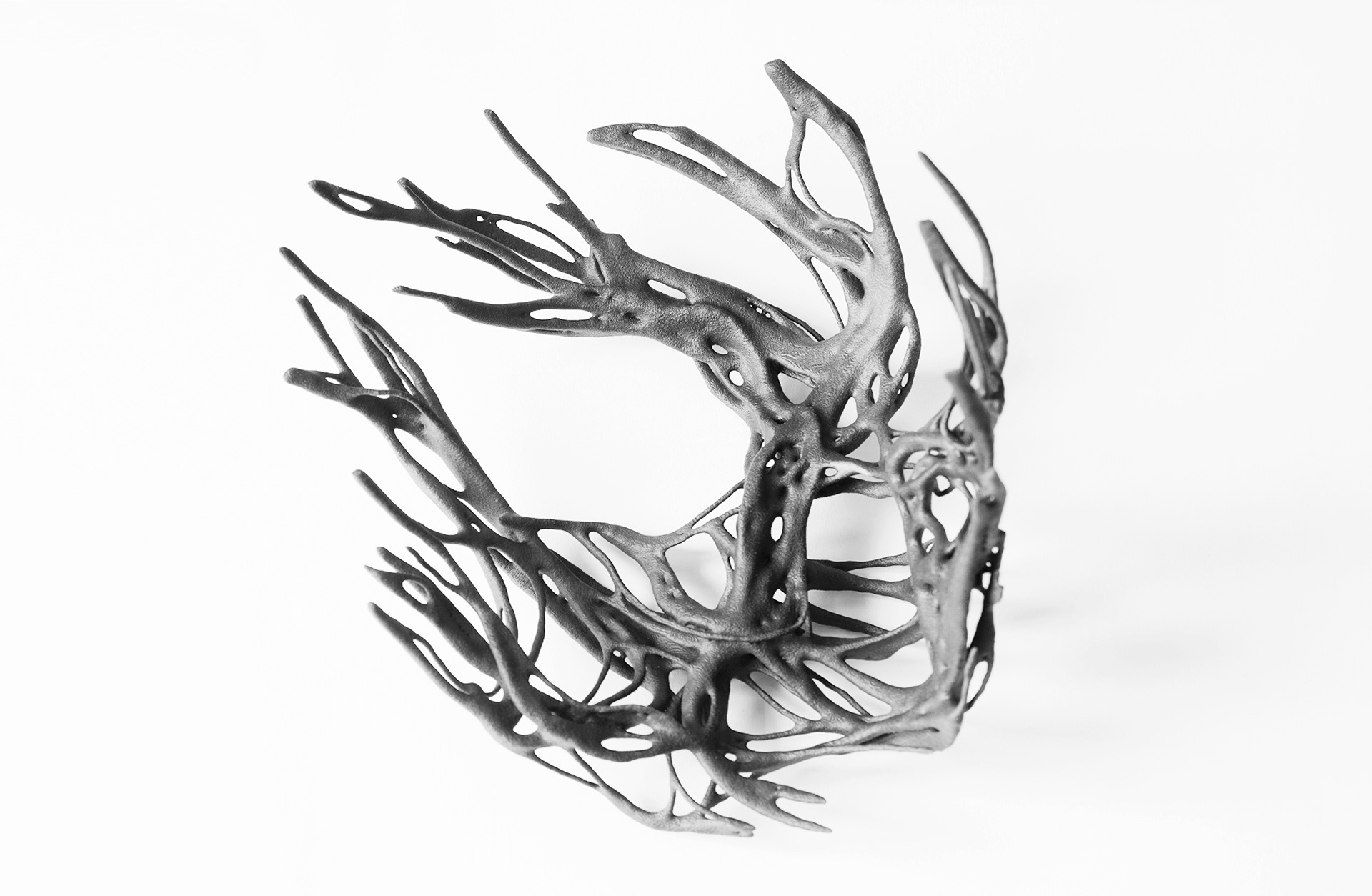
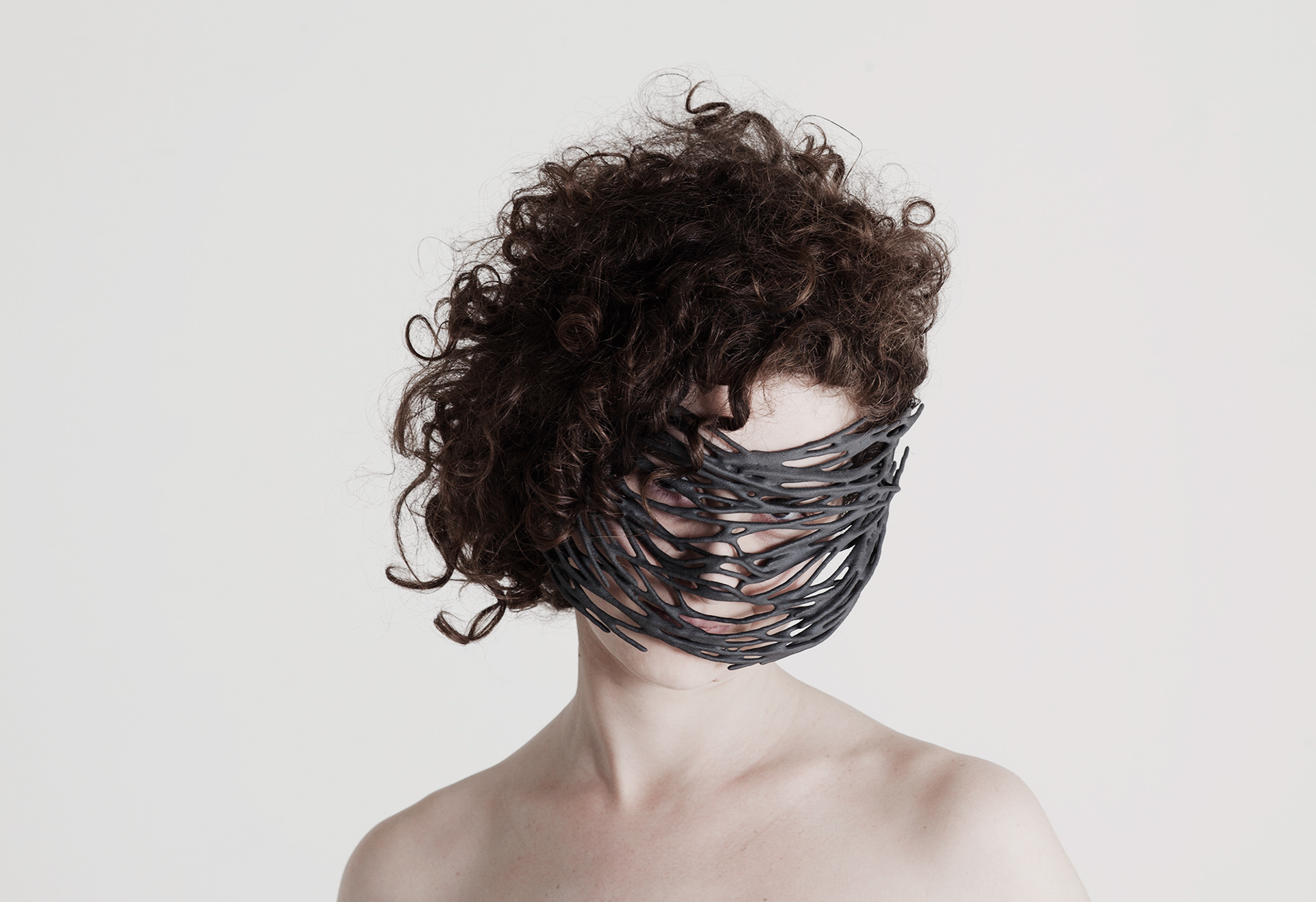
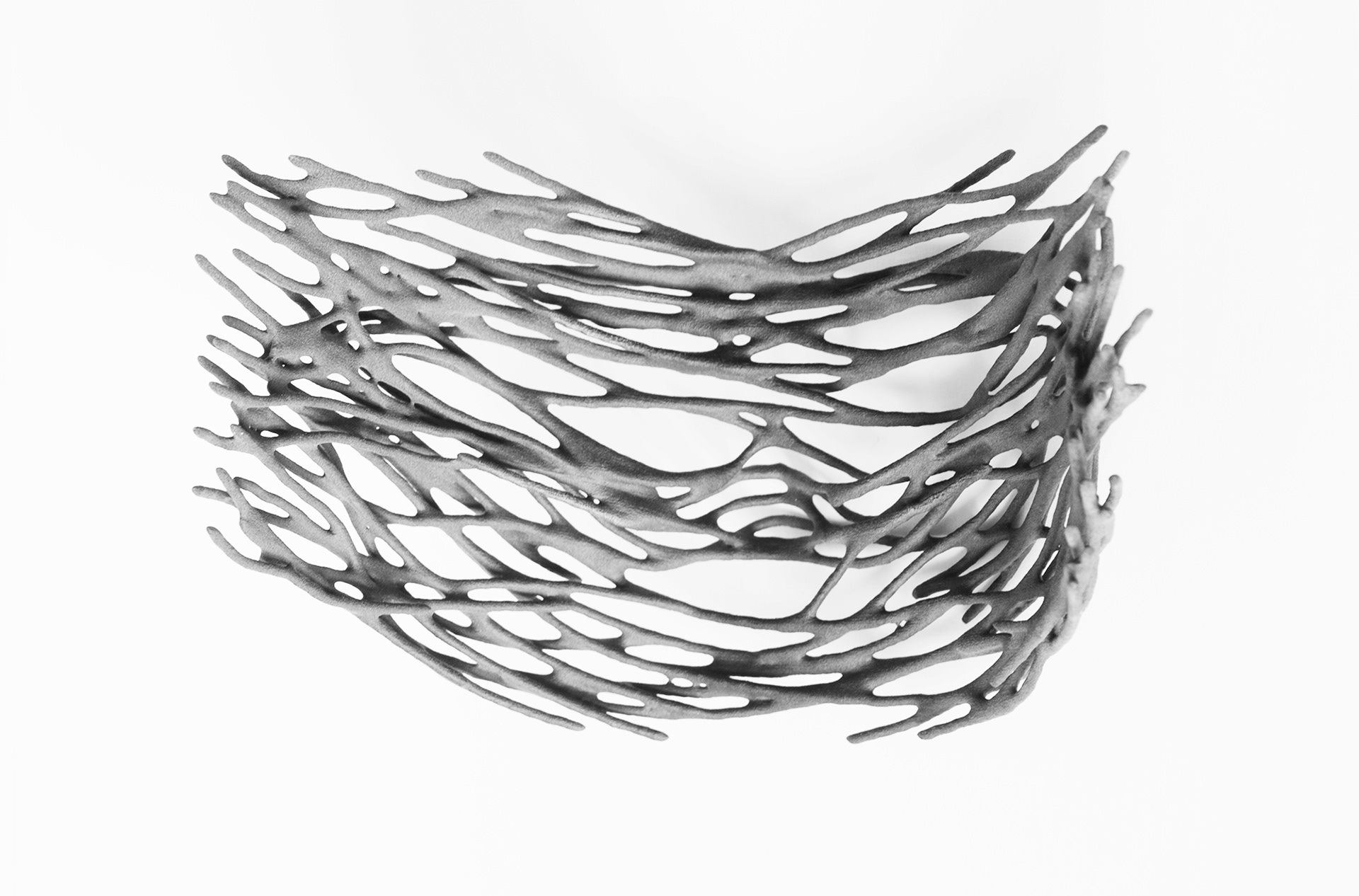
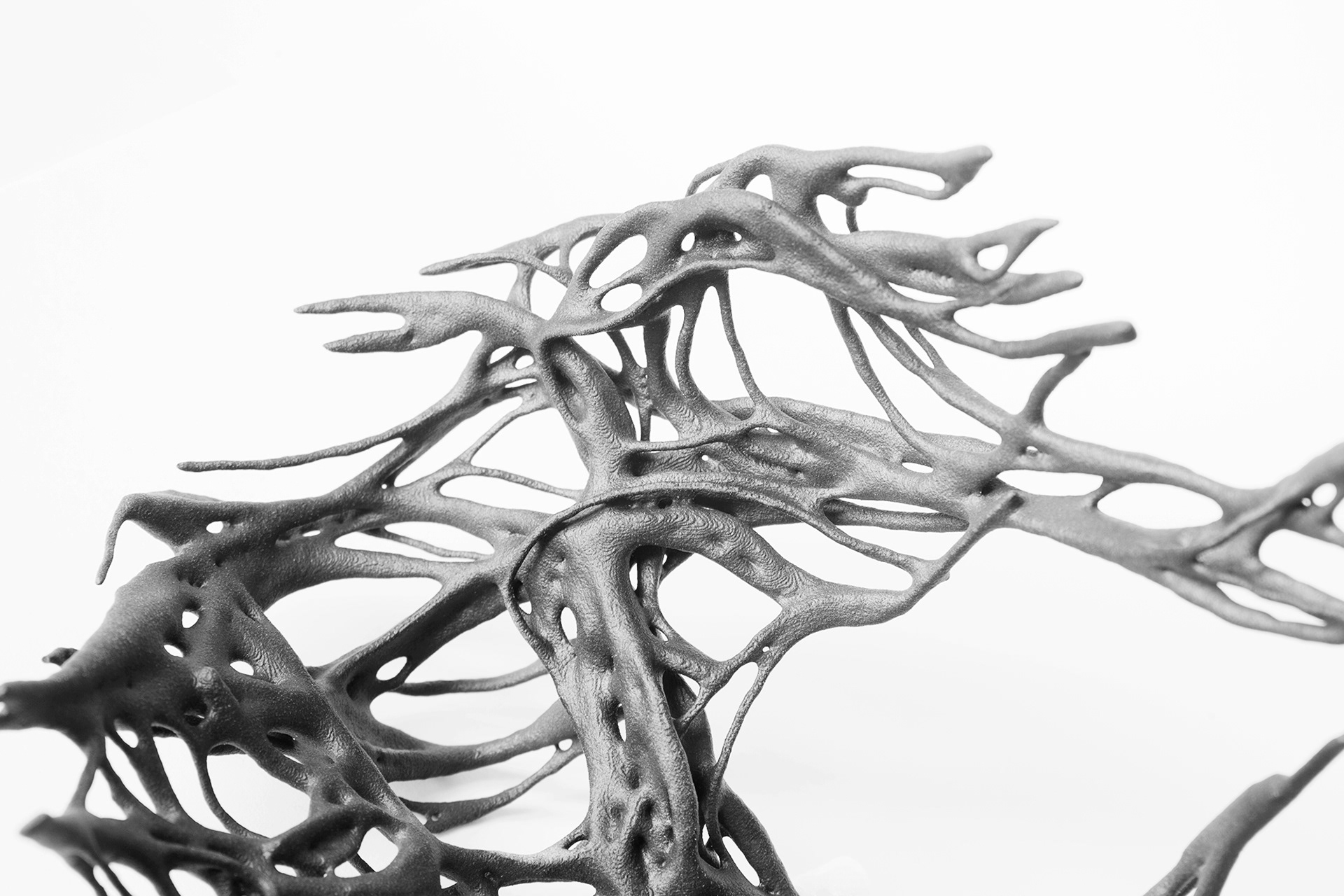
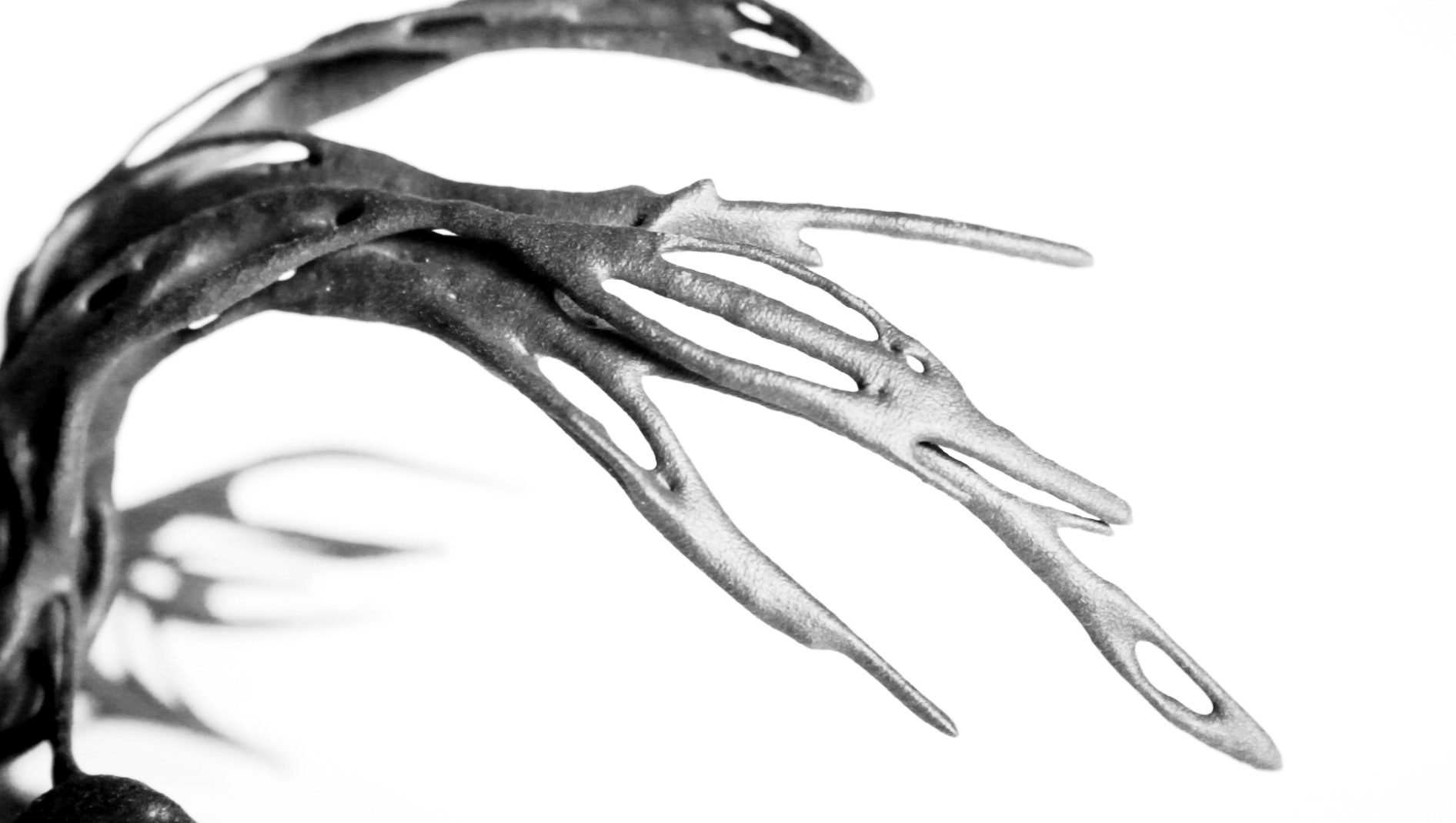
Collagene is a collection of fibrous masks designed using an independently developed software application that integrates body scanning, generative algorithms and 3D printing.
The project was initiated by MHOX as part of a year-long, EU-funded research program for innovative start-ups in the Emilia-Romagna region of Italy (2012–2013). It constitutes the main demonstrator of an art-driven innovation initiative, proposing an integrated system for mass customisation of wearable products, through 3D scanning of the human body, generative design of digital models, 3D printing of the products. The project investigated the integration of these new technologies to propose a scenario where wearable products are tailored to the unique anatomies of individual wearers, instead of coming in a limited number of sizes.
Artistically, the project explores postnatural visual languages, challenging the conventional distinction between natural and artificial, material and digital, human and non-human, while radically rethinking the relationship between the human body and technology.
The creation of a collection of masks offers an opportunity to rethink the relationship between the human body and wearable artifacts, envisoning them as the product of the growth of a digital organism on the topographic anatomy of the human body. The object keeps its traditional functions of body prosthesis, providing identity alteration and concealment, stimulating imagination, feelings and visual associations.
The project explores the boundary between physical and digital realms, connecting the abstract logic of computer code with the intimate, visceral dimension of bodily alteration that masks inherently embody. The topographic anatomy of the human body serves as input for a set of generative algorithms, that create the fibrous tissue of the masks. Once printed, these material formations perfectly fits its anatomical substrate.
The resulting collection comprises a population of differentiated individuals - phenotypes derived from a shared genotype. Regardless of how many masks are produced, they all share the same genetic code. This system offers significant flexibility, enabling a wide range of formal variations to adapt to different individuals and to reflect the vision of various designers.
The masks are produced using additive manufacturing technology, also known as 3D printing, and WINDFORM materials provided by CRP Technology in Modena (Italy).
This production technology is seamlessly integrated into the design strategy, enabling the creation of an extensive set of unique objects, each different from the other, of with highly intricate geometries.
The 3D printing material, WINDFORM LX 2.0, is a black polyamide-based composite reinforced with glass fibre Widely used in high-performance industries such as motorsport and aerospace, it combines aesthetic appeal with durability. It retains its chromatic properties over time and exhibits impressive mechanical characteristics, enabling the production of complex geometries without the risk of breakage or deformation. Additionally, its texture feels comfortable on the skin, making the masks suitable for extended wear.
This production technology is seamlessly integrated into the design strategy, enabling the creation of an extensive set of unique objects, each different from the other, of with highly intricate geometries.
The 3D printing material, WINDFORM LX 2.0, is a black polyamide-based composite reinforced with glass fibre Widely used in high-performance industries such as motorsport and aerospace, it combines aesthetic appeal with durability. It retains its chromatic properties over time and exhibits impressive mechanical characteristics, enabling the production of complex geometries without the risk of breakage or deformation. Additionally, its texture feels comfortable on the skin, making the masks suitable for extended wear.
This project proposes a new concept of the object: moving away from standardised models that are identically reproduced in limited sizes, to embrace open processes of mass customisation, and the production of unique, personalised pieces.
Through 3D printing and CNC fabrication techniques, the form, structure, colour, size, ergonomics, and pattern of the objects can be radically adapted to individual preferences and anatomical features.
Through 3D printing and CNC fabrication techniques, the form, structure, colour, size, ergonomics, and pattern of the objects can be radically adapted to individual preferences and anatomical features.
The software application driving this process is developed using Processing, an open-source programming framework based on Java. Body scan are conducted with a Kinect sensor, that captures both topographic and chromatic data from the models and integrates them into the digital environment. The mask design begins by tracing lines on the digital facial models, generating a network of curves that form the basis of the fibrous system. From these data, the application generates the 3D geometry that constitutes the final mask.
CREDITS
design: MHOX
research and coding: Filippo Nassetti, Alessandro Zomparelli
masks design: Mario Da Deppo, Filippo Nassetti, Alessandro Zomparelli
fabrication: CRP Group, WINDFORM
models: Lucio Pedrazzi, Silvia Tagliazucchi, Maria Regina Tedeschini
make-up and dresses: Laura Bedosti, Lucia Raffaelli
photographic support: Studio 129, Stefano Paolini
soundtrack: NONIMA - protozoa, ONO - difference
video production: MHOX